Welding WPS Explained: Key Elements and Advantages for Your Welding Procedures
Welding WPS Explained: Key Elements and Advantages for Your Welding Procedures
Blog Article
The Ultimate Overview to Welding WPS Procedures: A Detailed Review for Welders
In the intricate world of welding, Welding Procedure Specifications (WPS) work as the backbone of making sure high quality, uniformity, and safety in welding procedures. Recognizing the nuances of developing, applying, and keeping an eye on WPS treatments is vital for welders aiming to raise their craft and satisfy sector standards. As we delve into the various parts of a WPS and discover the ins and outs of certification and certification, we will discover the essential duty these treatments play in the realm of welding. Let's get started on a journey to unwind the intricacies and importance of WPS procedures in welding methods.
Value of WPS Procedures
Understanding the relevance of Welding Procedure Requirements (WPS) procedures is crucial for guaranteeing the high quality and stability of bonded frameworks. WPS procedures act as a roadmap for welders, describing the needed actions, criteria, and materials called for to attain an audio weld. By sticking to WPS guidelines, welders can guarantee uniformity in their work, resulting in structurally sound and dependable welds.
Among the primary reasons WPS procedures are vital is their function in keeping weld top quality and honesty. Complying with the defined welding parameters and methods laid out in the WPS helps avoid defects such as porosity, splitting, or insufficient fusion, which can compromise the toughness and sturdiness of the weld. Additionally, WPS treatments are important for making certain conformity with market requirements and codes. By complying with well-known WPS standards, welders can demonstrate that their job meets the required demands for safety and top quality, giving guarantee to customers, inspectors, and regulative bodies. In essence, the importance of WPS treatments can not be overemphasized, as they are essential to accomplishing constant, premium welds that fulfill market criteria and specifications.
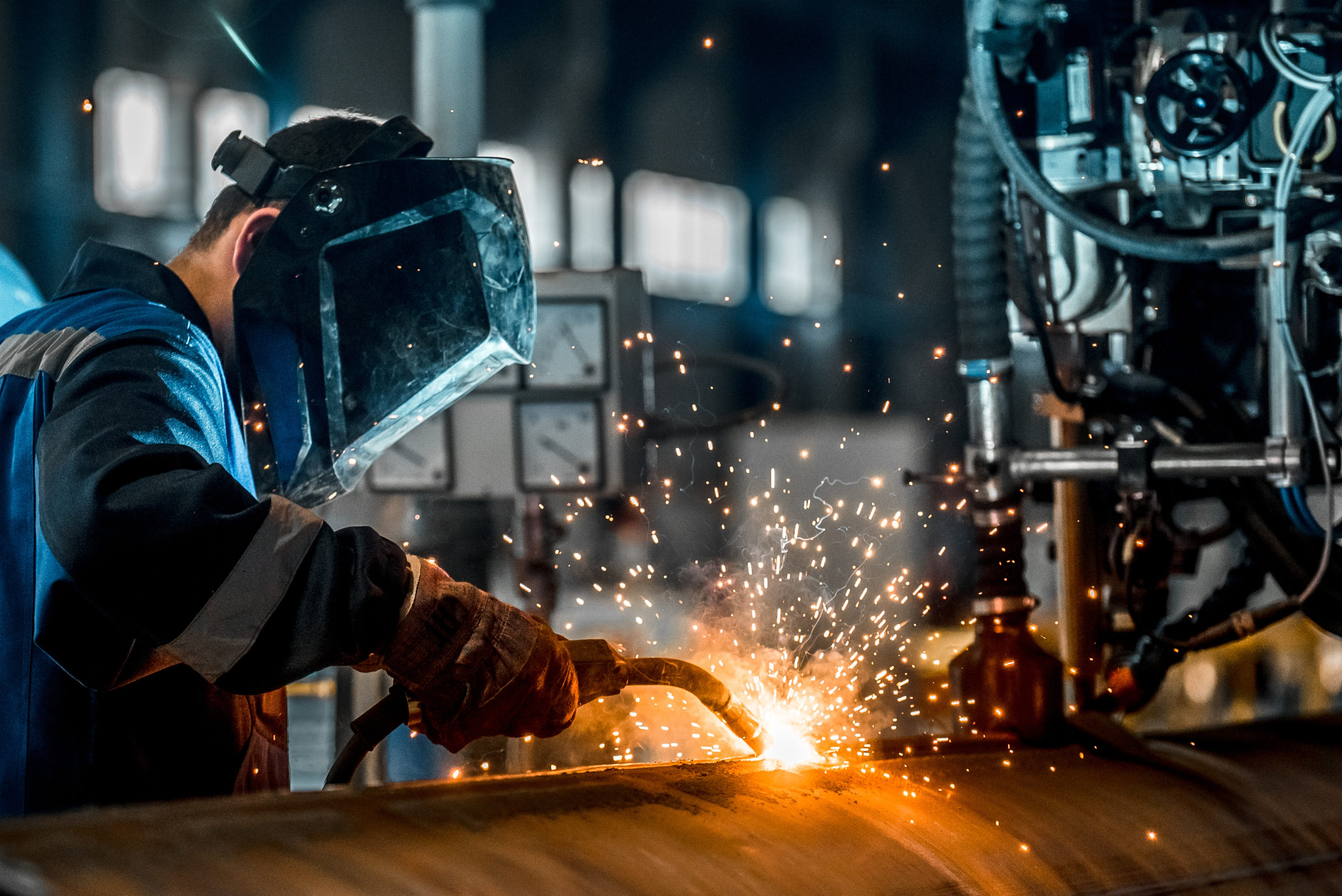
Elements of a WPS
A Welding Procedure Spec (WPS) generally comprises necessary elements that detail the particular demands for performing a weld, ensuring consistency and top quality in the welding procedure. The crucial elements of a WPS include essential variables such as base metals, filler metals, interpass and preheat temperatures, welding processes, shielding gases, welding positions, and post-weld heat therapy demands.
Base steels refer to the materials being joined, while filler metals are used to fill up the space in between the base metals throughout welding. The welding procedure outlines the certain method to be utilized, whether it's gas metal arc welding (GMAW), shielded metal arc welding (SMAW), or an additional method. Welding placements specify the orientations in which welding can be performed.

Credentials and Qualification
Having established the important elements of a Welding Treatment Specification (WPS), the emphasis now changes in the direction of the vital aspects of qualification and certification in welding techniques.

Certification, on the various other hand, is the official acknowledgment of a welder's qualifications by a pertinent accreditation body or organization. Welding accreditations are typically based on the certain welding processes, products, and settings a welder is qualified to deal with. Holding a valid welding accreditation shows that a welder meets industry requirements and is experienced to carry out welding jobs to the needed requirements.
Producing a WPS
To create a Welding Treatment Specification (WPS) that fulfills sector standards, mindful consideration of welding processes, materials, and functional criteria is vital. The very first step in producing a WPS is to determine the welding process to be used, such as gas metal arc welding (GMAW) or protected steel arc welding (SMAW)

Executing and Monitoring WPS
Upon completing the extensive Welding Procedure Specification (WPS) that thoroughly details welding processes, materials, functional specifications, and top quality guarantee procedures, the focus moves to effectively implementing and keeping an eye on the recognized treatments. Application entails guaranteeing that all welders associated with the task are familiar with the WPS and follow it meticulously during the welding procedure. This requires offering ample training and guidance to ensure adherence to the defined treatments. Monitoring the WPS includes constant oversight to verify that welding activities line up with the recorded specs. Evaluations, testing, and high quality control procedures are necessary components of the tracking process to recognize any type of issues or inconsistencies immediately. Normal audits and evaluations of the welding procedures aid in maintaining uniformity and go to this website quality throughout the project. Reliable execution and monitoring of the WPS are essential for guaranteeing the stability, strength, and safety and security of the bonded joints, inevitably adding to the overall success of the welding job.
Conclusion
To conclude, understanding and complying with Welding Treatment Specs (WPS) is essential for welders to guarantee high quality, consistency, and safety and security in their work. By understanding the parts of a WPS, acquiring proper qualifications and accreditations, creating thorough procedures, and applying and monitoring them efficiently, welders can improve their skills and proficiency in welding practices. Sticking to WPS treatments is important for producing top notch welds and conference industry requirements.
In the elaborate world of welding, Welding Procedure Requirements (WPS) offer as the foundation of guaranteeing quality, uniformity, and safety and security in welding procedures. The welding process outlines the certain technique to be used, whether it's gas metal arc welding (GMAW), shielded metal arc welding (SMAW), or another approach.To establish a Welding Procedure Specification (WPS) that meets industry standards, cautious consideration next page of welding processes, products, and functional parameters is important. The first step in producing a WPS is to identify the welding process more tips here to be utilized, such as gas metal arc welding (GMAW) or secured metal arc welding (SMAW)Upon completing the detailed Welding Procedure Specification (WPS) that meticulously details welding procedures, materials, functional specifications, and top quality assurance steps, the emphasis changes to effectively executing and keeping track of the well-known treatments.
Report this page